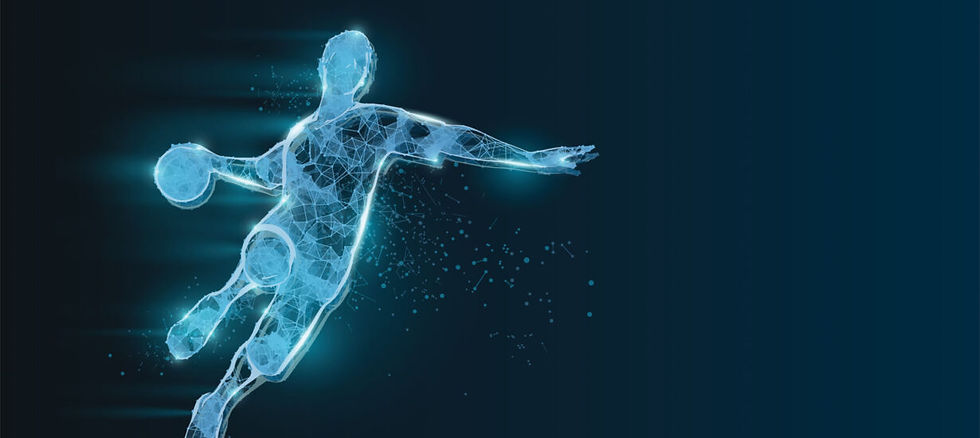
Running your machines at 50% utilization is a different ball game than running them at 70% utilization.
Most manufacturers are operating at 30-40% and getting to 50% is quite simple. Often times it requires uncovering bad habits that have developed over time and recapturing uptime.
This is easily done with real-time machine data. Once completed, you continue to use the data so those bad habits don't creep back in.
Manufactures are happy to gain this extra 5-10% b/c it doesn't require much change and it can happen quickly... as in days.
On the other hand, high performance manufactures that wanna get beyond the 50% and really maximize productivity know it requires more.
But is it worth it?
Operating at 70% utilization requires a team effort, collaboration, candidness, and a healthy culture. You can immediately feel this when you walk into a shop that's running at a high level of efficiency. HINT: buyers feel it too.
The value of operating at 70% is so much more than what OEE measures and Kaizen events provide.
Insights derived from machine monitoring play a pivotal role in increasing machine utilization and improving overall manufacturing operations in several ways:
1. Immediate Issue Resolution: Real-time monitoring allows manufacturers to identify and address issues as they occur, reducing the impact of problems on production. This proactive approach minimizes downtime, prevents bottlenecks, and maintains smooth operations.
2. Optimized Machine Usage: With real-time data on machine performance, manufacturers can make on-the-fly adjustments to optimize machine usage. This includes adjusting machine speeds, settings, or schedules to maximize output without compromising quality.
3. Resource Allocation: Real-time information helps manufacturers allocate resources more efficiently. For example, if one machine is experiencing delays, resources can be redirected to other parts of the production process to maintain overall efficiency.
4. Data-Driven Decision Making: Real-time insights enable data-driven decision-making at all levels of the organization. Managers can make quick, informed choices to address production challenges and improve processes.
So sure, you can use real-time data to uncover immediate benefits, but the thriving manufacturing business uses it for far more so they can transform their shop into a highly efficient operation.
Is it worth it to your business, let's talk?