Choosing the right machine tracking solution for your manufacturing operation is essential for maintaining productivity and efficiency. In today’s fast-paced industrial environment, businesses face increasing demands and competitive pressures. This article explores how to select a machine tracking solution tailored to your specific needs.
Understanding Machine Tracking Solutions
Machine tracking solutions capture data related to machine performance and operations. These systems can range from simple applications that log machine use to comprehensive management platforms offering advanced analytics and real-time monitoring. For instance:
Basic Solutions: May offer features like real-time tracking or simple notifications for maintenance needs.
Advanced Solutions: Could include predictive maintenance, integration with ERP systems, and customizable reporting dashboards.
By identifying which features are most beneficial for your business, you can narrow your choices. For example, a textile manufacturer may prioritize real-time tracking to quickly address machine downtime, while an automotive company might opt for predictive maintenance to prevent costly production delays.
Assessing Your Current Operations
Before exploring machine tracking solutions, evaluate your current operations. Start with a clear overview of the machines you currently use, their performance metrics, and the specific challenges that arise during tracking.
Consider the size of your operation as well. A standalone workshop might require a simple application to track one or two machines, while a large-scale production facility handling hundreds of machines would benefit from a more complex system capable of managing large volumes of data effectively.
Evaluating Integration Capabilities
Integration is key when selecting a machine tracking solution. Many manufacturing businesses use software for inventory management, production planning, and maintenance scheduling, such as SAP or Oracle.
Choose a machine tracking solution that integrates seamlessly with your existing systems. For example, if your inventory system automatically updates when machines operate, you will reduce manual entry and highlight potential stock shortages early. Ensure the new solution can share data effectively to enhance overall efficiency and minimize the learning curve for your team.
Future-Proofing Your Solution
When making a selection, think about future growth and technological advancements. A scalable solution is vital in today's ever-changing market, allowing you to adapt as operations grow.
For instance, if your business is planning to expand operations, a scalable machine tracking solution enables you to add more machines or features without overhauling the entire system. This adaptability can save you time and costs in the long run, ensuring that your system remains relevant.
Budget Considerations
Cost plays a significant role in decision-making. However, it’s important to assess the total cost of ownership beyond the initial investment. This includes:
Subscription fees
Maintenance costs
Potential integration modifications
For example, if a solution costs $10,000 to implement but requires $2,000 annually for support, understanding these costs will help you budget accordingly. Prioritize features that provide the highest value while fitting comfortably within your financial plan.
Gathering Feedback from Your Team
Involve relevant stakeholders in your decision-making process. Gather insights from operators, maintenance teams, and IT staff. They may provide valuable input regarding daily challenges or essential features.
By considering team feedback, you can refine your requirements and increase the likelihood of successful implementation. Employees will feel more invested in the new system, leading to higher adoption rates.
Testing and Trials
After narrowing down your machine tracking solution options, request demonstrations or trial periods from vendors. This allows you to test functionalities in a real-world setting.
During testing, focus on usability, reliability, and the level of support from the provider. For example, if a system boasts ease of use but exhibits frequent downtime during trials, it may not be reliable for long-term use.
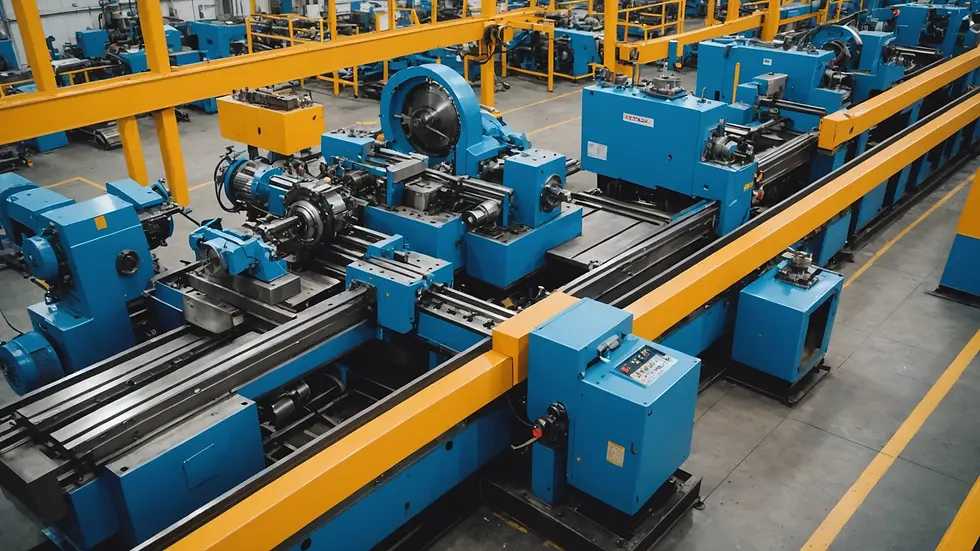
Monitoring Implementation Success
After implementation, it is vital to continuously monitor the effectiveness of your machine tracking solution. Establish specific success metrics. These could include:
A target of reducing equipment downtime by 20%
Increasing performance tracking accuracy to 95%
Regular monitoring helps identify areas for improvement and ensures the system meets your ROI expectations. Provide feedback to the provider to refine features or explore integrations that enhance performance.
Selecting the Right-Sized Machine Tracking Solution for Your Manufacturing Business
Selecting the ideal machine tracking solution is a detailed process requiring careful consideration of several factors. By understanding your operational needs, evaluating integration and scalability, assessing costs, collecting team feedback, and continually monitoring success post-implementation, you can secure a solution that fits perfectly.
Taking the time to research and reflect will streamline your tracking processes and prepare your business to thrive in an evolving manufacturing landscape. Whether you are a small workshop or a large production facility, having the right machine tracking solution is crucial for maximizing operational efficiency and achieving business success.