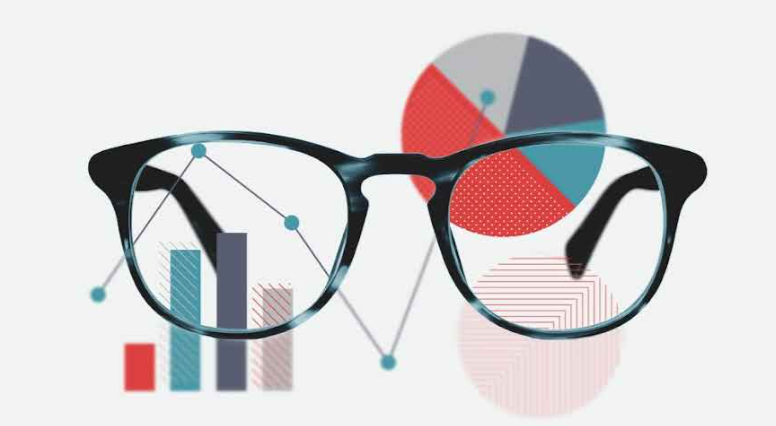
What's Worse Than Having No Data? Having Data No One Sees.
Making data visible in manufacturing plants directly affects your bottom line through faster problem detection and improved equipment maintenance. Production teams with instant access to performance metrics can prevent small issues from becoming costly breakdowns that halt operations.
Your operators can spot concerning patterns and take action immediately instead of spending hours searching through paper records or scattered files. Plants using clear data visibility systems cut their response times from hours to minutes, while maintenance teams stop equipment failures by catching subtle warning signs early. This hands-on method, powered by accessible performance data, reduces waste, improves production schedules, and keeps quality standards high. Your plant's success depends on having the right information at the right time.
Hidden Production Data Costs More Than Machine Downtime
When production information stays buried in paper records or scattered spreadsheets, plants lose money through delayed problem detection and missed chances to prevent equipment issues. You spend valuable time searching for answers while machines sit idle. Poor data access leads to reactive maintenance and quality control problems that drive up costs.
The Importance of Quick Access to Machine Performance Data
Production teams need quick access to machine performance data to spot problems early. Without it, small issues grow into major breakdowns.
Consider this real-world example: One manufacturing plant found operators spend two to three hours per shift just looking for basic performance data. This meant problems often went unnoticed until they caused significant downtime.
Moving from Reactive to Proactive Maintenance
Clear data visibility helps teams move from constantly fixing problems to preventing them. Paper-based systems and scattered spreadsheets create expensive bottlenecks. Manufacturing teams might spend hours tracking down information that should take minutes to find. This delays important decisions about maintenance and quality control.
Imagine a production line running slightly below optimal speed. Without easy data access, the small efficiency loss could continue for weeks before anyone notices the impact on output. The gap between when problems start and when teams discover them directly impacts the bottom line.
Spotting Early Warning Signs in Production Data
Early warning signs often hide in production data. A small change in machine performance might signal future problems, but if teams can't easily spot these issues, minor concerns become major repairs. Fast access to performance data helps teams make better decisions about when to schedule maintenance.
The Benefits of Improved Data Visibility
Manufacturing plants that improve data visibility and make data visible see quick results:
Teams can spot and fix problems faster
Small issues are prevented from becoming expensive repairs
Production schedules are optimized and waste is reduced
The key is making information easy to find and understand. This creates a more proactive approach to managing production.
Real-Time Data Visibility Prevents Production Disasters
Real-time data gives floor managers instant alerts about machine performance problems, quality deviations, and resource usage. This allows them to make fast decisions to prevent costly downtime.
Quick Adjustments and Optimization
Managers can quickly adjust production settings, deploy maintenance teams, and optimize material flow. When supervisors see live data on their screens, they can spot trends before they become major problems.
Proactive Issue Detection
Smart sensors on production equipment can detect subtle changes in performance before failures occur. For instance, a motor might show increased vibration patterns or temperature spikes that indicate pending issues. Quality inspection systems can identify minor defect patterns in real time rather than discovering problems after a full batch is complete. This proactive monitoring helps spot issues when they are small and fixable rather than after they have caused significant waste or downtime.
Instant Decision-Making
Floor supervisors can now make instant decisions based on live data feeds:
When a machine shows signs of stress, they can immediately reduce speeds or adjust settings
Quality control teams receive instant alerts about defect patterns and can modify parameters on the spot
Maintenance teams get mobile notifications about potential issues and can respond before equipment failures
This quick response ability transforms reactive maintenance into productive prevention.
Dynamic Optimization
Live monitoring of overall equipment effectiveness helps managers fine-tune operations throughout the day. They can shift workers to different stations based on real-time bottlenecks. Material flow tracking ensures components arrive exactly when needed at each workstation. This dynamic optimization keeps production running smoothly and efficiently.
Managers can also spot opportunities to improve processes as they happen rather than waiting for end-of-shift reports.
Real-World Results
A manufacturing facility that implements real-time monitoring saw the response time to quality issues drop from hours to minutes. Their system now alerts operators about minor variations in production specifications, letting them adjust settings before making defective products.
Here's another example: the facility uses mobile alerts to notify maintenance teams about potential equipment issues. This helps them prevent unplanned downtime by addressing problems during scheduled breaks.
By making data visible in real time, manufacturers can proactively prevent production disasters. Instant alerts enable quick adjustments to avoid quality defects and equipment failures. Dynamic optimization keeps operations running efficiently. Implementing real-time monitoring transforms reactive problem-solving into proactive prevention that minimizes waste and maximizes productivity.
Clear Data Displays Drive Better Shop Floor Decisions
Simplified data displays can significantly improve your shop floor operations. When operators can easily see and understand performance data, they make better decisions. Visual indicators show exactly when action is needed, allowing supervisors to spot issues faster with clear performance dashboards. New employees also learn their jobs more quickly when standards are shown visually. These improvements lead to more confident operators and better productivity overall.
Empowering Operators with Visual Control
Visual displays give operators direct control over their work areas. Check out these examples:
Color-coded status lights show machine conditions at a glance
Simple performance gauges help operators know immediately if they're meeting targets
When problems occur, step-by-step visual guides show exactly what actions to take
This puts problem-solving power directly in the operators' hands rather than waiting for supervisors to intervene. The result? Operators who feel more ownership of their work and make decisions with competence.
Transforming Team Management
Clear data displays also transform how supervisors manage their teams. Digital dashboards provide instant visibility to every work cell status, with performance trends appearing as simple line graphs that highlight patterns. Team metrics display in easy-to-read formats that show who needs support.
This visibility lets supervisors spend less time gathering data and more time coaching their teams. They can quickly spot areas that need attention and provide targeted help to specific operators or processes.
Accelerating New Employee Training
Visual work instructions and performance standards speed up new employee training as well. Picture-based guides show proper procedures without language barriers, while performance targets appear as simple gauges that new operators easily understand.
When issues arise, troubleshooting flows as visual decision trees guide operators to solutions. This visual approach helps new employees build confidence faster, as they learn independently by following the cues rather than constantly asking for help.
Real-World Results
Manufacturing facilities using visual management systems report significant improvements. Take this machine shop, for instance: a visual display helped operators track their own efficiency scores, leading to self-directed improvements and better production rates.
Here's another example. A facility used visual work instructions to reduce new hire training time. Their picture-based guides enabled employees to learn tasks 20% faster.
As these examples show, when you make data visible through clear displays, you give teams the tools to improve on their own. Operators gain more control over their work, supervisors can manage more effectively, and new employees get up to speed faster. Implementing visual management systems on your shop floor can drive better decisions at every level.
Data Sharing Barriers Break Team Communication
When departments can't share data easily, it creates ripple effects across the organization. You make decisions with incomplete information, workers enter the same data multiple times, and reports show different numbers for the same metrics. These barriers slow down production planning and make it harder to schedule maintenance, causing quality issues to take longer to fix.
The Compounding Effect of Poor Data Sharing
Picture a manufacturing plant where the morning shift discovers a machine calibration issue but can't easily notify the afternoon team. The problem persists until someone finally picks up the phone or sends an email that gets noticed. Poor data sharing creates a compounding effect of delays, forcing you to wait longer to make important decisions as you gather information from multiple sources. Workers waste time entering the same information into different systems, with each department maintaining their own spreadsheets and databases. This leads to confusion about which numbers are correct, and monthly reports often show conflicting data because each team pulls information from different sources, making it hard to track performance and spot trends.
Communication Gaps Between Shifts
Communication gaps between shifts create ongoing challenges. For instance, the morning team might solve a production problem but have no easy way to share the solution with the evening shift. When similar issues occur, the evening team starts from scratch. Root cause analysis becomes difficult because teams can't easily access historical data, and problem solving takes longer because information is scattered across different systems and departments. Teams spend more time searching for information than fixing issues.
A Real-World Example
A furniture manufacturer faced these exact issues. Their design team used one system while production used another, causing customer specifications to often get lost between departments. The consequences were significant:
Orders took longer to complete
Quality issues increased
After creating a shared data system to make data visible, teams could see real-time updates. The results were impressive:
Order completion time improved
Quality problems decreased because everyone worked with the same information
Multi-shift operations became smoother because each shift could easily see what happened on previous shifts
Turn Your Machine Data into Production Results
Your machine data contains the solutions to increase output, reduce waste, and stop downtime - but only if your teams can access and use it. Moving from scattered spreadsheets to clear data displays creates immediate improvements in production.
Our team brings 20 years of proven experience building data visibility systems that work in manufacturing environments. We guide plants through practical steps to turn machine data into measurable results. Schedule a plant assessment today and see how our approach can improve your operations within 90 days.